It’s a common sight at any industrial park, but five open loading dock doors in front of a moody OSHA inspector could land your company a $63,375 fine!
The rules have changed. Welcome to 2017.
If your company hasn’t been waiting on bated breath for the latest regulations, on January 17 OSHA added wording to statute 1910.28. All unprotected sides and edges suspended 4 feet or more in the air must have approved fall protection in place. Violations could cost as much as $12,675 per occurrence.
Either word hasn’t travelled fast enough, or many businesses are ignoring the new regulation.
Driving through an industrial park last week I stopped counting the open loading docks when I ran out of fingers. By my calculation, 1/3 of the open dock doors were compliant, 1/3 had inadequate fall protection, and 1/3 had no fall protection at all. An overzealous OSHA inspector could take the same drive I did and rack up fines in the hundreds of thousands without leaving the comfort of his air conditioned Prius.
Who isn’t getting a raise this year, because Johnny left the dock door open on a hot day?
Every year Fall Protection is the number one hazard cited by OSHA. Of the 6,906 citations issued related to Fall Protection in 2016, most came from the residential construction industry (roofing). OSHA’s top priority is to get these numbers down, but the new rules are hitting general industry in ways many are not aware of - and in more ways than just loading docks.
OSHA’s new ruling requires edges 4 feet or more in the air to have one of three methods of protection:
- A guardrail system
- Safety net system
- Personal fall protection
For loading docks, practicality eliminates a safety net and personal fall protection system. That leaves two options:
- Keep the loading dock doors shut when the truck is away
- Install an OSHA approved guardrail system.
Don’t expect a thin chain or strip of highlighted caution tape to do the job. The guardrail must be able to take up to 200lbs of horizontal pressure and be highly visible. Two or more chains MAY be acceptable if they are spaced at both a “high” and “mid” tier level and visible, but the single chain is not kosher.
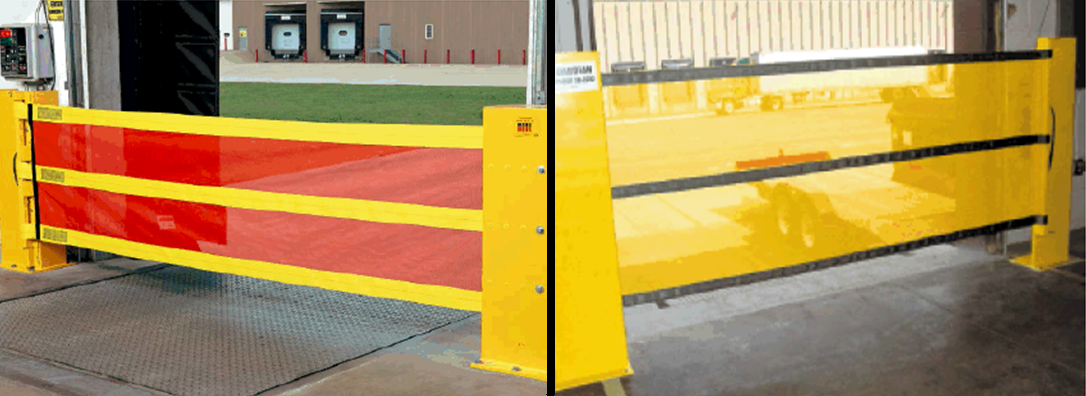
If keeping dock doors shut at all times isn’t practical, there are still many ways to stay OSHA compliant. The ideal solution might look like a Rite-Hite Dock-Guardian Safety Barrier which can handle up to 30,000lbs of horizontal pressure and is highly visible. Other methods used include a Vestil Safety Swing Gate or Uline Scissors Security Gate.
Another target of the January 17 language is guarding on fixed ladders. Stationary ladders must have a guard at their opening in order to be complaint. OSHA would frown on the ladder below.
Safety chains atop fixed ladders may have been okay in the past, but are now out. To remain complaint a spring loaded self-closing gate is needed. The reasoning behind this decision is that a safety chains do not close themselves. They require a worker to stand on the ladder while using one hand to reattach the chain with his back is to a hazard. A self-closing gate requires no such action and is OSHA compliant.
Fall protection is not required when using portable ladders however, OSHA still encourages employers to provide additional protection.
The January rule changes also call for a Walking Worker Surfaces Inspection. These inspections are to be done “on a regular schedule” and “when necessary”. These inspections are to be adequate enough to identify slip, trip, and fall hazards. Employers are mandated by the new rules to have a scheduled WWS inspection and to conduct more when conditions or events occur that warrant an additional check.
Don’t let OSHA catch you with a naked loading dock. Slip, trip, and fall regulations have been revised and employers are responsible for keeping up with the language. Especially when a violation is visible from the roadside, it’s probably worth fixing right away.