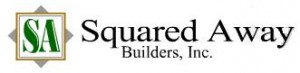
Like many young companies in the construction industry Squared Away Builders, Inc. concentrated on working hard, staying busy and taking care of their customers. This left little or no time to manage other things like workman’s compensation insurance premiums. In the case of Squared Away, learning how to manage workers compensation insurance was one key to lowering costs, making the company more safe and enabling the company to become proactive instead of reactive when it came to workman’s comp.
A feeling of helplessness…
“When it came to work comp there was an inherent feeling of helplessness” says Brett Wittig, President of Squared Away Builders, Inc. “As a small business you try to do the best you can managing your employees while managing your business for profit at the same time and when the WC premium rolled around it felt like a slap in the face. We had been working hard all year, concentrating on the basics of running a business and it felt like we were helpless and couldn’t do anything about this large premium.”
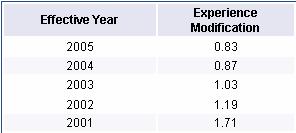
We didn’t know what was coming…
“After our third year in business, we knew our modifier was 1.71 but we had no idea where this number came from, how it was determined or how it affected our premiums directly. We did know however after three years of large premiums that we had to do something to lower our costs if we wanted to stay competitive.”
The search for knowledge…
“Frustrated about work comp but still trying to concentrate on making a profit and taking care of our employees Bill Katzfey caught our attention. His philosophy of creating a knowledge based culture change in our organization in order to help manage work comp costs was something that Squared Away needed. What’s more important was that Bill was able to give us the knowledge, specifically in regards to the construction industry, which we needed as a company in order to make that culture change. R&R Insurance Services has given us and continues to give us a solid understanding of what it truly costs to have an injured worker”, states Dan Wittig, Operations Manager.
The difference it has made…
“We have had the program we designed with the knowledge and techniques provided by R&R for three years now and we finally are seeing the benefits. We have used the premium savings to invest in our employees and in the future of our company. There is no doubt in my mind that we would not be in the position we are in today without the help and knowledge of R&R Insurance Services has provided us.”
“Since 2001 we have been applying the concepts that R&R teaches in their WC seminar. It took a lot of hard work, consistent communication of a solid message and a little patience.”
Brett & Dan Wittig
Squared Away Builders